Asset Integrity of Valves and Bolted Connections
Status: AWARD END DATE: 03/31/2022
Background:
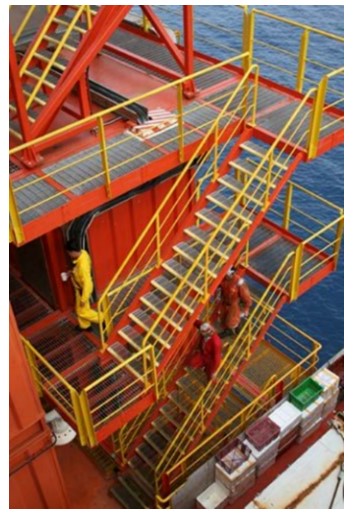
Offshore drilling activities over the last decades have left thousands of offshore platforms in bad condition and abandoned because of impropriate maintenance and operation. This is in part due to the expense and time-consuming nature of manual inspection and maintenance in the remote offshore environment. Those offshore platforms will not only be re-used in renewable energy sector (thermal, offshore wind, and tidal), but also in space sector. For example, the offshore platform could be used by NASA or space tech companies for rocket launching and landing pads. Some reported news indicate that Space-X will reuse the existing offshore platforms as spaceports for its re-usable rockets. Timely inspection and maintenance of the existing offshore platform is of great interest of Texas economy. To extend the lifetime of existing platforms, timely inspection and maintenance of platform infrastructures are of great importance. Among those critical components in offshore operations, 1) valves and 2) bolted connections are high priority to assess for failure. One of the challenges in valve operation is the valve's failure caused by rust. Mild rust can cause the valve's rough operation. Excessive rust may lead to permanent structural damage and cause serious leakage. Preventing a valve's failure requires regular inspection and maintenance. As most of the platforms are designed with a limited area and multi-level structure (Fig. 1), an unmanned ground vehicle (UGV) should be capable of making a small radius turning and climb up/down stairs to qualify the job. Tapping and listening, also called percussion, is an intuitive way to detect structural abnormality, which has been used by us to invent a new approach to monitoring the looseness of bolted connections.
To extend the lifetime of existing platforms, timely inspection and maintenance of platform infrastructures are of great importance. Among those critical components in offshore operations, 1) valves and 2) bolted connections are high priority to assess for failure.
One of the challenges in valve operation is the valve's failure caused by rust. Mild rust can cause the valve's rough operation. Excessive rust may lead to permanent structural damage and cause serious leakage. Preventing a valve's failure requires regular inspection and maintenance. As most of the platforms are designed with a limited area and multi-level structure (Fig. 1), an unmanned ground vehicle (UGV) should be capable of making a small radius turning and climb up/down stairs to qualify the job.
Tapping and listening, also called percussion, is an intuitive way to detect structural abnormality, which has been used by us to invent a new approach to monitoring the looseness of bolted connections.
Additional Media Assets:
Industry Impact:
A timely inspection of infrastructure, especially topside valves in platforms are thus the key to extend the lifetime of an offshore asset. Current inspection techniques often involve trained human operators and requires excessive amounts of time and money. With state-of-the-art robotic and inspection technologies, such limitations may be remediated and a much-needed extra layer of safety will be added. Robotic enabled valve maintenance not only reduces costs and increases accuracy, but also prevents workers from contacting the leaking valves. Robots do not experience fatigues or loose concentration and can work continuously, and in general robotic approaches are effective and less prone to error.
Combining this work with percussion holds much potential in monitoring the looseness of subsea bolted connection due to its simplicity and suitability with robotics integration.
Project Goals:
The goal of this project is to develop transformative robotic valve inspection technology that will lead to a time efficient and cost-effective system for valve inspection and maintenance which can extend the life cycle of existing oil platforms. Through the proposed autonomous robotic system (i.e., autonomous ground service) equipped with valve operation and inspection tool, valve anomalies due to mechanical failures will be detected at early stages, which allows operators to make informed decisions on maintenance and repairs of abnormal valves.
This project will also develop robotics enabled percussion approach to subsea connection inspection. Since the Grayloc clamp connectors, with the advantages of compact design, are commonly used in oil and gas industry, in this research both flange type and Grayloc connections under the submerged condition will be experimentally studied. Via a remote operated vehicle (ROV) that is equipped with a hydrophone, a visual-servoing system, and a percussion component, we can detect bolt looseness in subsea flanges and Grayloc connections.
Tasks:
This research includes the following specific tasks:
- Develop a ground service robot that can climb stairs and track lanes in oil platforms
- Develop a valve inspection tool that can detect stuck valves while operating them
- Develop a vision-based lane tracking for the robot to track lanes in oil platforms
- Develop a vision-based recognition algorithm to locate valves for inspection
- Develop a machine-learning based underwater percussion method
- Develop a tapping and listening device to enable percussion based bolted structure inspection
- Conduct comprehensive testing after integration of key components
Ultimately, the project will push the boundaries of what can be accomplished by integrating robotics and structural health monitoring technologies.
Gantt Chart:
Highlights:
- Set up testbed and designed new tool for valve operation and inspection
- Demonstrated the percussion method for monitoring flange looseness is effective for under water application
- Demonstrated stair climbing using mobile platform
- Fabricated and tested a new tool for valve operation and inspection
- Programmed a Husky unmanned ground vehicle
- Tested YOLO algorithm for valve detection
- Conducted more test of percussion based bolted structure inspection
- Fabricated a robotic tapping device
- Set up a (32' long x 16' wide x 4.3' deep) research tank for comprehensive testing
Key findings:
- Developed a mobile platform which can climb stairs
- Developed>Developed a valve operation and inspection tool
- Developed a visual serving control for the mobile platform to track the detected lane
- Developed a machine learning based valve detection algorithm
- Developed a machine learning approach to train in-air and in-water impact-induced sound signals
- Developed a deep learning approach to train in-air and in-water impact-induced sound signals
- Classified flange looseness status to five classes using the proposed approaches